Repair or Replace Plant Equipment? Exploring the Ultimate Hidden Factor
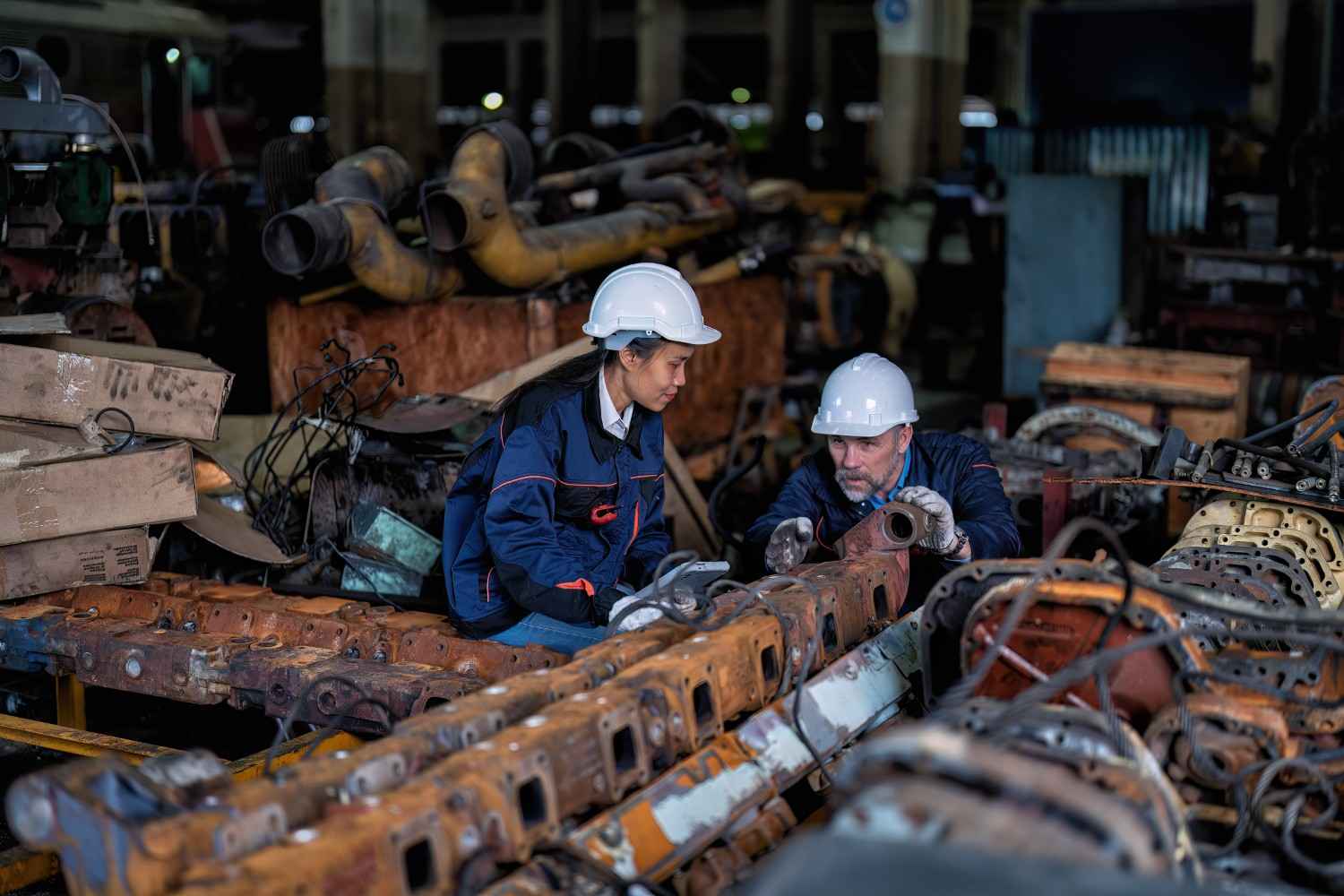
When faced with a malfunctioning or outdated piece of machinery, plant managers, maintenance engineers, and operations supervisors often find themselves pondering the age-old conundrum of whether to repair or replace plant equipment.
But what if the commonly discussed factors like cost, downtime, and long-term efficiency weren’t the only things you needed to consider?
Most existing guides focus on predictable elements like maintenance costs and the quality of repairs. While these are vital, they miss addressing one hidden factor that could profoundly affect your decision-making process; not only for now but for your business’s future.
This post will uncover the often-overlooked role of operational alignment when deciding to repair or replace plant equipment and offer actionable insights for plant professionals seeking optimal long-term solutions.
Alongside this distinct perspective, we’ll briefly touch upon standard considerations to provide a comprehensive framework.
Why Operational Alignment Matters More Than You Think
Operational alignment refers to how well your equipment integrates with your current workflows, processes, and future technological advancements.
Many decision-makers fail to assess whether a machine, after repair or replacement, will seamlessly “fit” into the larger structure of the plant’s operations.
Imagine investing in a replacement machine with state-of-the-art interface capabilities. However, upon installation, you find that it doesn’t sync with your legacy software. Now, you’re faced with additional costs for software upgrades or compatibility workarounds.
This scenario is a classic case of poor operational alignment.
Benefits of Considering Operational Alignment
Before breaking down steps to assess this factor, here’s why it’s critical:
- Maximised ROI (Return on Investment): Machines that integrate smoothly require fewer adaptations, extending their operational efficiency.
- Reduction of Silos: Well-aligned equipment enhances collaboration between departments, especially maintenance and production teams.
- Future-Proofing: Equipment designed to work with upcoming technologies avoids obsolescence, saving significant costs in the long term.
Operational alignment could mean the difference between just a short-term fix and achieving sustainable success.
How to Assess Operational Alignment for Repair or Replacement
1. Study Current Processes
Begin by analysing how the equipment fits into existing workflows. If you’re considering a repair, assess whether the repaired machine will continue supporting critical processes without gaps. If replacement is on the table, check whether new equipment will complement existing machinery and software systems.
2. Anticipate Future Operational Needs
It’s important not only to evaluate today’s requirements but also to anticipate the plant’s future priorities. Are there plans for automation, IoT integration, or energy efficiency adoption? If so, prioritise replacements that align with these goals.
Example Checklist:
- Does the equipment allow for easy integrations with other software or hardware used in our plant?
- Is it scalable for future production growth?
- Will training demands for employees increase considerably?
3. Evaluate Compatibility with Maintenance Strategies
Will your team find it easier to maintain after a repair or learn to operate a new replacement machine? Replacement often comes with hidden costs such as extensive training or overhauling your maintenance schedules. Ensure either option fits seamlessly into proactive maintenance practices like predictive or preventive strategies.
4. Factor in Sustainability Goals
Operational alignment also extends to environmental sustainability. Does the replacement equipment reduce CO2 emissions or energy consumption? Sustainability should no longer be an afterthought but a primary consideration for longevity and regulatory compliance.
5. Consult Stakeholders Across Departments
Highly-aligned equipment decisions require insights from everyone affected, including:
- Production Teams (for output synchronisation)
- IT (for software compatibility)
- Maintenance Staff (for long-term upkeep feasibility)
Standard Considerations with a Fresh Perspective
While operational alignment is crucial, understanding the traditional repair/replace factors can’t be overlooked. Below is a fresh take on key points commonly found in blog posts:
1. Equipment Repair Costs
Yes, initial repair costs may be cheaper, but don’t just think about the current need. Pair repair cost analysis with alignment evaluations. If the equipment is misaligned with future goals, sustaining yearly repair costs could undercut your budget.
2. Downtime and Productivity Losses
When considering downtime for repairs, also examine whether operational misalignments during this period could worsen productivity post-repair.
3. Long-Term Efficiency
A repaired piece of equipment may perform adequately if aligned with the plant’s existing technology. However, if misaligned upgrades become necessary, your financial forecast may face turbulence.
4. Disposal Costs for Old Equipment
Beyond direct disposal costs, consider if disposal leaves workflow gaps that cost production or operational capacity.
5. Employee Retraining for Replacement
Training costs are standard, but the extent to which operational alignment reduces learning curves can save weeks, eliminating delays in production schedules.
Don’t Overlook Predictive Analytics in Decision-Making
Predictive analytics tools and CMMS (Computerized Maintenance Management Systems) bring data transparency by tracking repair history, energy consumption, and operational efficiency.
Use them to determine if repairing supports productivity precision or if a new tool simplifies plant-wide integration.
Examples of tools to consider include:
- IBM Maximo or Coast CMMS for maintenance data alignment
- Predictive systems integrated within AI dashboards for real-time tracking
A Real-World Operational Alignment Case Study
Take Premier Manufacturing as an example:
- The company faced ongoing failures with a conveyor system integral to production. Repairing it repeatedly seemed cost-effective.
- However, upon a comprehensive operational alignment review, they realised the repaired equipment was bottlenecking other IoT-advanced systems.
- A replacement designed for scalable, automated processes allowed seamless integration, reducing downtime from 15% to 3% annually while cutting electricity costs.
This stark improvement showcases how operational alignment decisions can significantly outperform traditional considerations.
Final Thoughts on Repair vs Replace
Deciding to repair or replace plant equipment is one of the most challenging tasks for plant managers and maintenance engineers.
While traditional factors like cost and efficiency are heavyweights in this decision, overlooking operational alignment can create unexpected inefficiencies or set future limitations on growth and innovation.
Think beyond quick fixes and prioritise equipment that supports your plant’s overarching goals for production, technology, and sustainability.
Align your decisions with both short- and long-term ambitions to optimise the time, money, and output of your plant equipment.
Take Action
Struggling with operational alignment decisions? Enabling predictive alignments may sound complex, but tools like CMMS or consulting with maintenance analysts can simplify the process. Future-proof your plant today with smarter tools and better strategies.